Tuning pianos
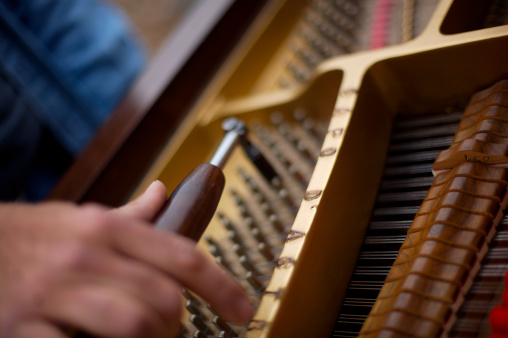
Tuning a piano means tuning about 250 strings at the right frequency. Tuning exists for each string but not only, also in relation to all the others.
Therefore, even a microscopic reduction of tension – and therefore of frequency ratio and sound pitch – will cause a faulty relationship of one string with all of the remaining 249 ones: it follows that, in a tuning session, a technician tuner “fixes” not only 88 keys but more than 60,000 relations between strings.
Micro-losenings occur essentially already in a short-time period from tuning, but the sum of these shifts reaches, after a year of average use of the instrument, a bad level to good musical achievement, though luckly the user’s ear does not suffer from a change that takes place so slowly and gradually over time.
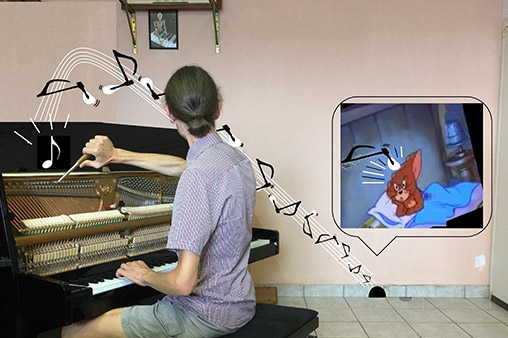
The operation involves changing strings tension in order to restore:
- the pitch of the reference sound (tuning fork or chorister)
– the note having as reference the frequency of the tuning fork determines the pitch of all notes of the keyboard. This pitch should be the same for all instruments so that they can also play simultaneously. Continuous micro-adjustments of the structure of the piano and the strings tend to lose the tension given to the same strings and consequently the pitch of the tuning fork decreases – - the proper relationship between the sounds, dictated by the laws of Equal Temperament
- the purity of the sounds of the individual keys, reached by tuning strings that are beated by the same key
Marco Grassi performs the tuning with “Technique to Ear” which is based on direct perception of sound without relying on electronic instruments. This is made possible thanks to an “absolute pitch”, that is not relative but “beat-related”, percieving all beats between sounds. By calibrating the beats that occur between the notes of the scale, the tuner defines with absolute precision the pitch of the individual sounds of the scale itself, under the laws of equal temperament, or, when required, of other temperaments.
Piano tone
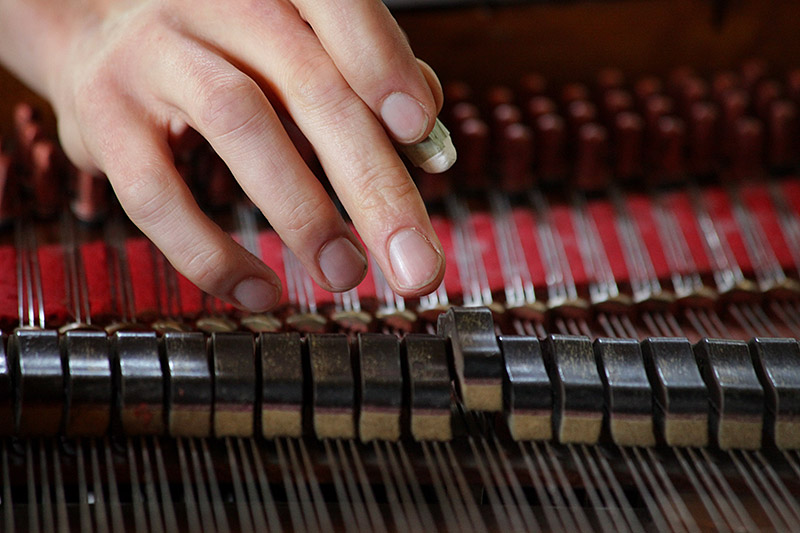
Playing a well-tuned piano but not harmonized is like singing the right notes but with an unpleasant voice.
The tone, which stands àfrom tuning, is a complex operation that is used to change the color of the sound, not his pitch.
This gentle practice, generally little known to users and at times even to pianists, must be exercised by professional technicians. It expected to work directly on the hammers and more precisely on the felts. Various tools are used including the “intonator”, with a handle of thin needles, that are ranging wisely sunk in the felts themselves.
The main objectives of this work are:
- obtain an objectively beautiful sound, suitable to the client’s taste, in harmony with the acoustic environment.
- broaden the range of dynamic possibilities from “pianissimo” to “fortissimo”.
- get “Opening” tone during a crescendo towards the “fortissimo”
The progressive modification of the stamp with increasing intensity is a peculiar characteristic of the piano and contributes to emphasize the transition between “piano” and “forte”.
Adjusting the piano mechanism
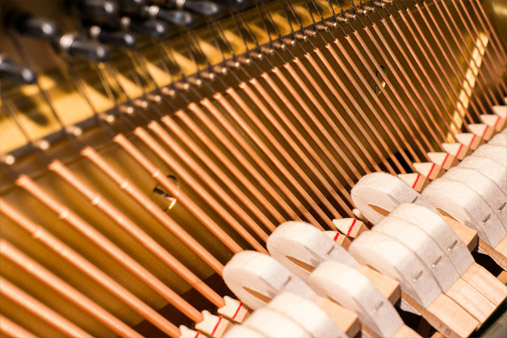
The mechanical system of the piano keyboard itself has a multitude of possible settings.
With use, the status of these adjustments tends to slowly move away from the ideal situation. Acting through them, the tuner restores the maximum yield of the mechanical condition of expression. This maximizes the amplitude of the range of dynamic possibilities, the speed for the trill and retorted, the “pianissimo” control.
Whenever the mechanism is excessively worn and through the regulation of the same is no longer possible to obtain a quality upgrade, another action is required…
Mechanical-piano keyboard system review
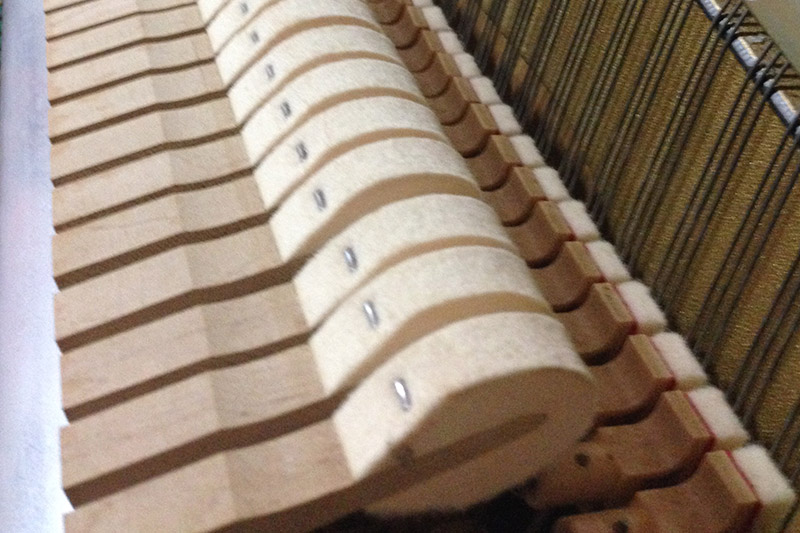
It involves the replacement of all parts having signs of wear and/or old age, in order to obtain the condition of a new unit.
For example if the hammers have already been repeatedly combed and have deep grooves, you will need to replace them or make them re-felting.
The new hammers when assembled are still treated in the laboratory with necessar pre-combing and pre-tuning.
They are also adapted to the tailpiece by placing them in an appropriate manner to it in order to make the most of the impact energy.
Like the hammers, all other parts are tested and replaced with new ones, the ones that can be reset to its original state are worked by hand.